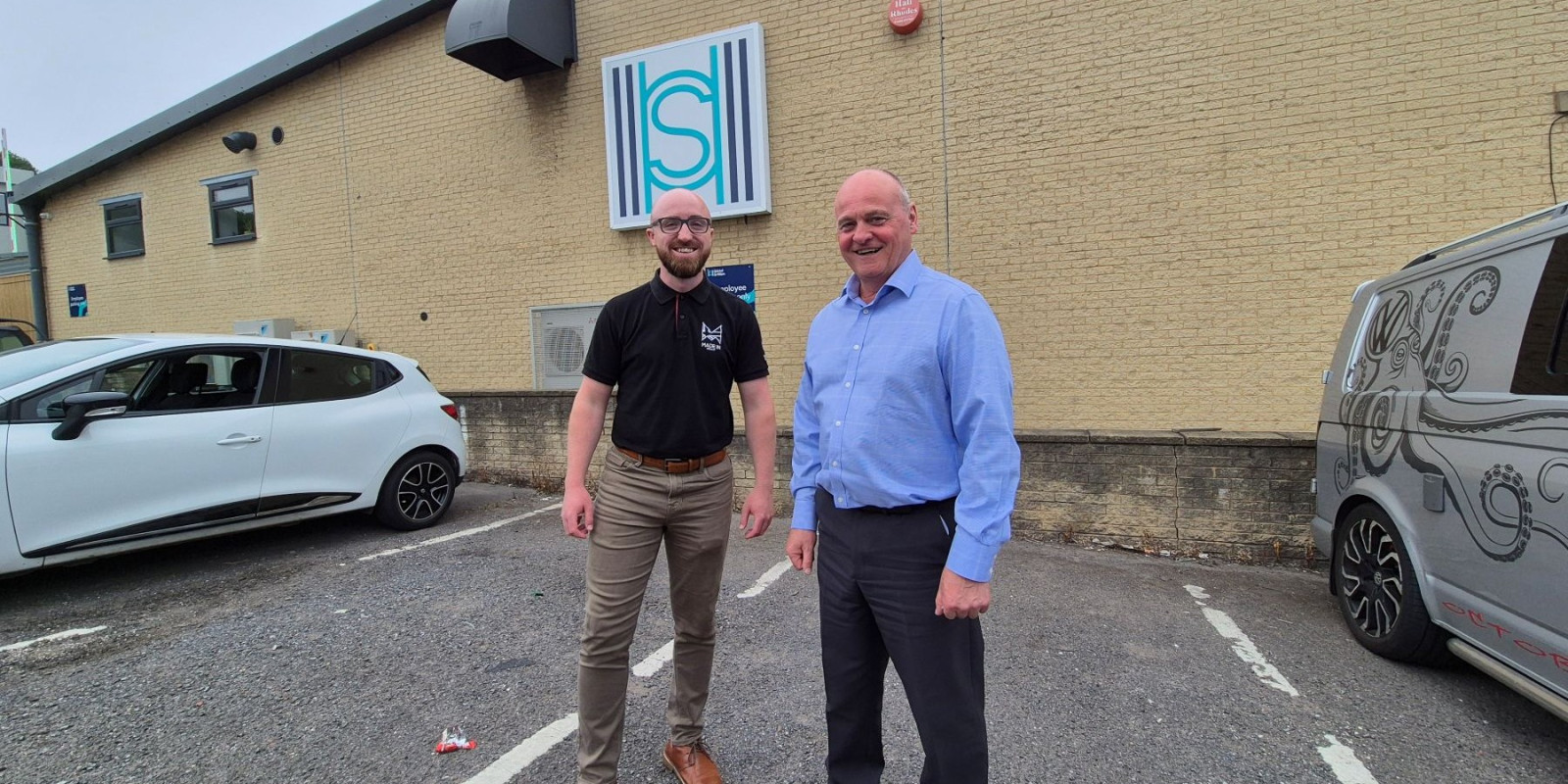
Why British Steel making – and British Industry – Must Be Protected
“A nation must retain the ability to produce its own steel and build its own ships — anything less is a relinquishment of sovereignty.”
Recently, we had the pleasure of welcoming Sam Sleight from Made in Yorkshire for an open, forthright discussion on the current challenges facing UK manufacturing.
Our Managing Director, Andy Dawson, was candid about the headwinds Siddall & Hilton (S&H) is navigating — and the steps we’re taking to build a more secure future.
Escalating Operational Costs
Our decision to transition to 100% renewable electricity — in anticipation of government emissions targets set for 2035 — reflects our commitment to environmental leadership. The Mayor of West Yorkshire, alongside regional leaders, has declared a climate emergency and set a science-based target for the region to achieve net zero carbon by 2038, with meaningful progress expected by 2030.
Aligning with these ambitions has increased our annual energy expenditure. Compounding this, a recent increase in National Insurance has imposed an additional six-figure tax burden. Unlike many international competitors who benefit from state subsidies on energy and labour, UK manufacturers are expected to absorb these rising costs independently — a growing disadvantage in an already distorted global market. Passing these costs on to customers is simply not a viable option.
People Power — Our Greatest Vulnerability
Despite offering skilled operatives upwards of £35,000 after two years’ training, finding and retaining talent is harder than ever. Our 12.8% turnover rate is below the national average, but every early departure represents months of lost training and thousands in wages.
The question lingers:
Is the next generation engaged enough for modern manufacturing?
How We’re Responding
Broadening the Recruitment Pipeline:
-
We are actively diversifying our recruitment strategies by:
Advertising in Bradford and other ethnically diverse areas to tap into a wider engineering talent pool. -
Partnering with agencies specialising in skilled migrant labour, known for high levels of commitment and productivity.
-
Exploring veteran and ex-offender employment programmes.
-
Supporting underrepresented groups through a fair work charter, living wage employer, wellbeing initiatives, flexible working and engagement practices.
Driving Culture Through Continuous Improvement
Andy’s leadership philosophy is simple but powerful:
“Today’s performance will not be acceptable Tomorrow, we simply must be better”.
We foster a culture of constructive challenge, inspired by Toyota’s “red-square” exercise. While we don’t adopt it verbatim, the principle remains: new starters are encouraged to speak up, critique processes — not people — and contribute to improvement from day one.
Investing in People
In the past year, we’ve invested £250,000 in a new welfare hub, complete with:
-
Air conditioning for hot-shift recovery;
-
On site showers, bicycle facilities and charging.
-
Electric car charging.
-
Bean-to-cup coffee machines;
-
A games area for informal team socialising.
-
An open suggestion wall, where all ideas are welcomed anonymously.
It’s more than a morale booster — it’s a performance multiplier.
The result? Faster changeovers, fresher thinking, and higher productivity.
The Power of Regional Networks
Our partnership with Made in Yorkshire — and the wider Made in Group — is invaluable. It amplifies voices like ours, shares best practices across hundreds of SMEs, and opens doors to talent pipelines no single company could develop in isolation.
The Path Forward
-
Champion a Fairer Trade Framework
Advocate for tariffs that align with the EU’s upcoming measures and a long-term industrial strategy that transcends electoral politics. -
Keep Investing – Even in Uncertain Times
Sustained investment in people and technology ensures tomorrow’s capacity is built today. -
Strengthen Regional Collaboration
Lean on — and contribute to — the local network that is making Yorkshire manufacturing impossible to ignore.
Our Commitment
We’ve been working with steel wire in Brighouse since 1895. Adaptability is part of our heritage — but resilience is multiplied when shared.
If your business believes in backing British manufacturing, we urge you to share your story. Together, we can stay in control of our industrial destiny — and, with any luck, ensure the next generation creates more than it consumes.