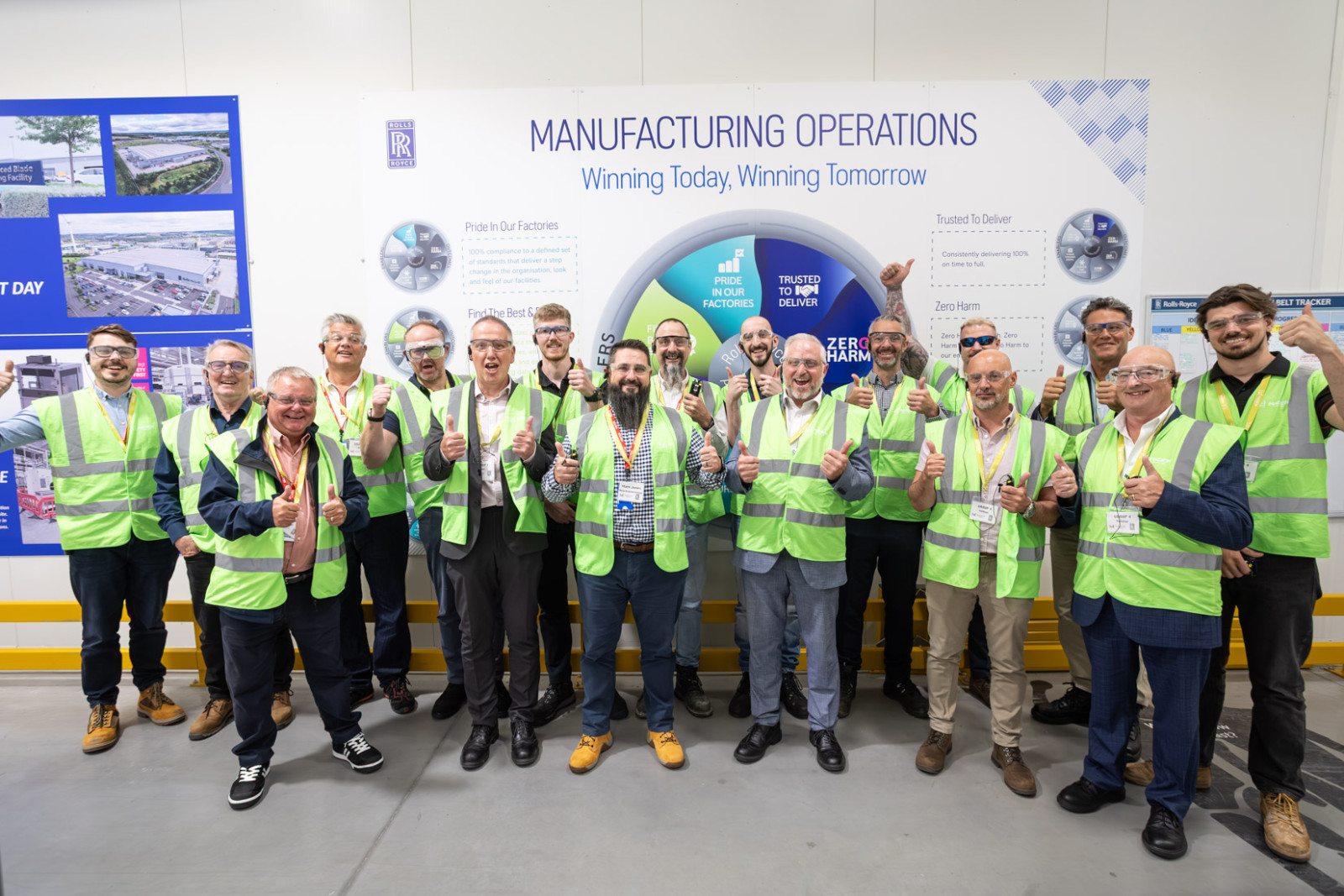
Inside the Innovation Engine: Made in Yorkshire Members Visit Rolls-Royce’s World-Class Facility in Rotherham
Last week, members of Made in Yorkshire were given an exclusive look behind the scenes of one of the UK’s most advanced manufacturing operations during a best practice visit to Rolls-Royce’s turbine blade casting facility in Rotherham.
The visit, part of Made in Group’s ongoing commitment to sharing knowledge and showcasing excellence across British industry, offered attendees unique insights into the scale, complexity, and innovation driving one of the world’s most recognisable engineering brands.
Rolls-Royce’s Rotherham site, known as the Advanced Blade Casting Facility (ABCF), plays a critical role in the company’s civil aerospace division. The factory specialises in the production of single crystal turbine blades – vital components that help power large commercial aircraft such as the Boeing 787 and Airbus A350.
Welcoming the delegation, Gary Train, Vice President of Manufacturing, offered a strategic overview of the organisation’s transformation journey. “We’ve been on a significant turnaround over the past 18 months,” Train explained. “From streamlining our operations to increasing performance and profitability, Rolls-Royce is now on a trajectory to become a high-performing business with an operating margin close to 15%.”
But the visit wasn’t just about the numbers. Members were treated to a compelling look at what makes Rolls-Royce a global leader, not least the incredible craftsmanship, high-precision engineering, and dedication to quality that underpin its products.
A Foundry with Ambition
The ABCF is currently undergoing rapid expansion, aiming to double its output over the next few years. Ian Bickley, Head of Manufacturing, explained how the facility plans to increase annual turbine blade production from 105,000 to 210,000 by 2027, a staggering scale-up effort that involves onboarding new machines, introducing new part numbers, and integrating a growing workforce.
“We’re going from 130 to over 220 direct operators in just 18 months,” Bickley said. “And it’s not just about people, it’s about culture. Everyone on the team needs to be aligned with our values if we’re going to meet the challenges ahead.”
That focus on people was a running theme throughout the visit. Rolls-Royce has launched a rigorous induction and training process for its workforce, some of whom originally come from non-engineering backgrounds. Former teachers, butchers, and care workers are now helping build some of the most complex engine components in the world, bringing fresh perspectives and a new sense of purpose to the shop floor.
Precision at Its Peak
Guests were then whisked off on a guided tour of the facility, each group accompanied by a Rolls-Royce chaperone. The route featured four stops, with a specialist speaker at every station, perfectly placed to share their know-how and give Made in Yorkshire members an inside look at the world-leading processes behind the Advanced Blade Casting Facility. From injecting wax around intricate ceramic cores, to building complex casting moulds, and finally using vacuum furnaces to create single-crystal components, every step underlined Rolls-Royce’s absolute dedication to the highest standard of quality.
A big thank you to our 4 expert speakers for delivering so much value on the day:
- Russell Bond, Manufacturing Engineering Manager
- Jayden Francis, Operations Manager
- Tom Harrison, Production Leader
- Alistair Buchanan, Business Technical Specialist Machining
During the tour, Bond explained how each blade operates in extreme conditions, temperatures exceeding the melting point of the metal itself, thanks to advanced cooling technologies and barrier coatings. “Think of it like spinning an ice cube in a 200°C oven at 40,000 rpm for 10 years and expecting it to still be an ice cube,” he said.
From advanced X-ray inspections to structured light 3D scanning, the quality control process is as advanced as the manufacturing itself. Non-destructive testing, dimensional analysis, and digital process monitoring all form part of a robust system designed to deliver precision-engineered components that literally keep aircraft in the sky.
Learning Through Best Practice
The Made in Yorkshire group is no stranger to factory tours, but the Rolls-Royce visit stood out for its blend of cutting-edge technology and grounded, people-first culture. Attendees were impressed not just by the technical prowess on display, but by the way the team integrates digital tools with hands-on craftsmanship.
“It’s great to see such an iconic company pushing boundaries while staying open to learning from others,” one attendee remarked. “They’ve embraced continuous improvement, lean principles, and a culture of accountability, exactly the kind of best practice we want to share within our own networks.”
Rolls-Royce’s leaders were equally curious about the wider manufacturing landscape. As Jayden Francis noted, the team joined Made in Yorkshire to benchmark themselves not only against other aerospace firms, but across the wider manufacturing ecosystem. “There’s always more to learn, and great ideas don’t just come from high-tech industries. That’s why groups like Made in Yorkshire are so valuable,” he said.
Looking Ahead
The visit wrapped up with an opportunity for informal networking over refreshments, offering members a chance to reflect on the day’s insights, forge new connections, and discuss shared challenges.
The Rolls-Royce site tour is just one of many events organised by Made in Yorkshire to build collective knowledge and encourage cross-sector collaboration. Through in-person factory visits, digital roundtables, and online thought leadership, the group helps promote British manufacturing excellence and strengthen the UK supply chain.
Next up is the National Online Meet-Up, where members will hear from three expert speakers discussing future-facing themes across industry. RSVP now via your member dashboard to secure your place, share your news, and contribute your own thought leadership to the Made Platform.