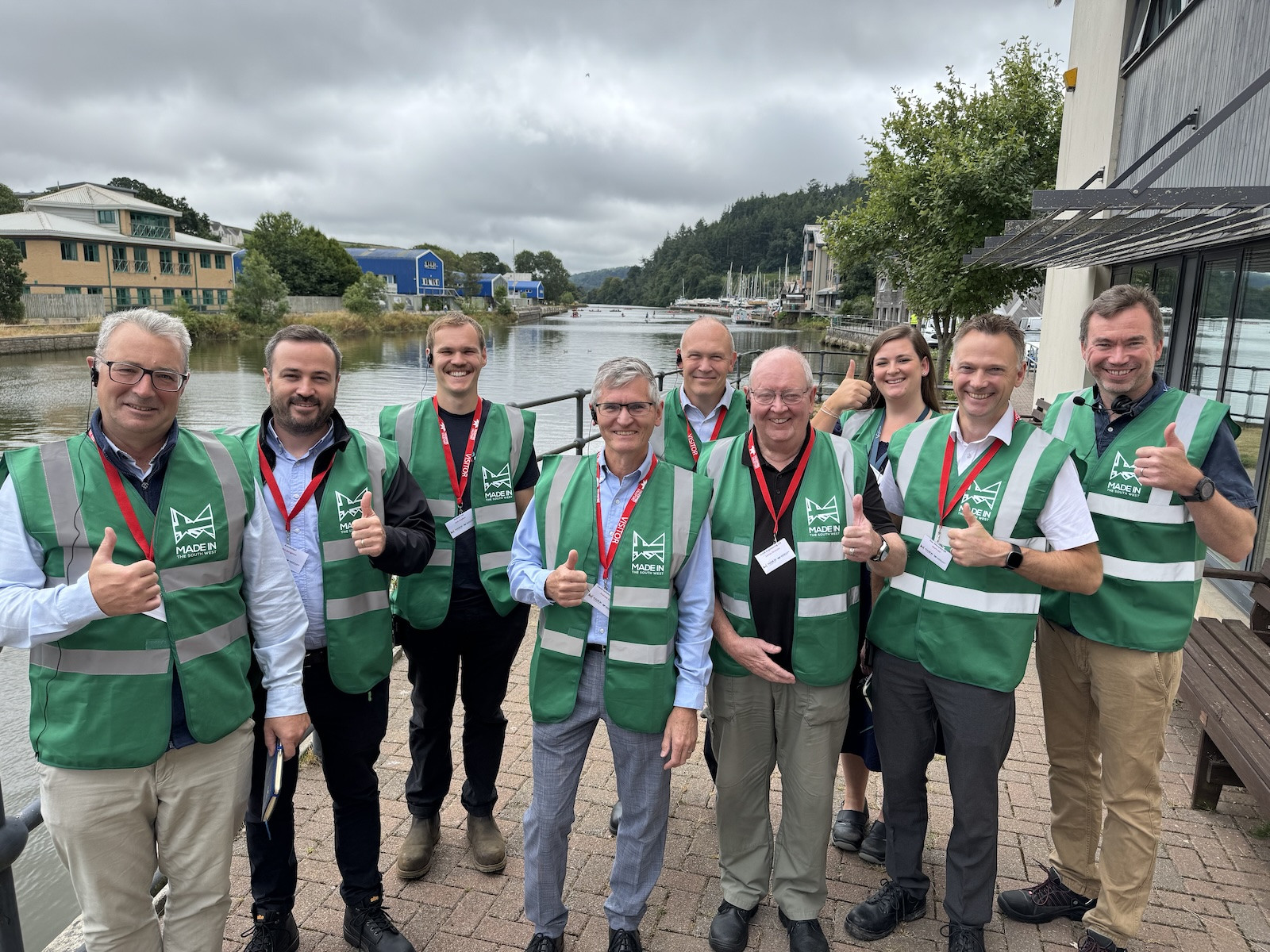
Inside Teledyne Valeport: A Best-Practice Beacon in Marine Instrumentation
Yesterday, Made in the South West held an inspiring factory tour at Teledyne Valeport Ltd, one of our founding members, based in Totnes, North Devon. The event provided a rare and valuable opportunity to gain an in-depth look at how this cutting-edge manufacturer designs and produces advanced instrumentation for the hydrographic, hydrometric, and oceanographic sectors.
The tour offered more than just a behind-the-scenes look, it was a showcase of what world-class British manufacturing looks like today: high-tech, people-first, and deeply committed to sustainability.
A Legacy of Innovation
Founded in 1969, Teledyne Valeport began with a simple yet effective mechanical flowmeter, its very first product used magnets and a reed switch to measure the flow of water. That early innovation soon evolved into directional flowmeters that helped assess the feasibility of large-scale projects such as the Thames Barrier.
Today, the company has grown into a global leader in precision marine instrumentation, supplying a vast range of clients—from universities and research institutions to offshore energy companies and water authorities.
Following decades of growth, Valeport relocated from Dartmouth to Totnes, expanding from one building to multiple facilities. By 2013, they had grown to 72 staff. In 2023, after more than 50 years as a family-owned business, the company was acquired by Teledyne Marine, part of the global Teledyne Technologies Group. The acquisition has gone smoothly, allowing the Valeport team to continue operating autonomously while benefiting from broader global support.
Best Practices That Set the Standard
Several best-practice elements stood out during the tour, especially for those interested in how modern manufacturers are integrating engineering excellence, sustainability, and workforce development.
1. Design-Led and Vertically Integrated
Teledyne Valeport designs all its own circuit boards, firmware, and software, as well as the mechanical and electronic architecture of its instruments. All calibration and testing is done in-house. While circuit board fabrication is subcontracted, the company retains full control of design and validation. This ensures speed, agility, and technical quality across the board.
2. People First: Developing Talent from Within
Employee development is a key part of the company’s DNA. Teledyne Valeport has never been without apprentices in its history, and many long-serving staff have risen from apprenticeship to management roles. The company supports training from entry-level through to degree apprenticeships and focuses on retaining talent for the long term.
3. Clear Communication and Collaboration
With just over 100 employees, the company regularly gathers its full team for ISO meetings, group discussions, and project updates. Having a space where all staff can meet together fosters transparency, teamwork, and a shared sense of purpose.
4. Sustainability in Action
Sustainability is embedded in day-to-day operations. Two of the company’s buildings are fitted with solar panels, and one is nearly self-sufficient. Valeport operates a full-spectrum recycling programme, from machine shop scrap to office waste. The company also aligns with Teledyne’s “40 by 2040” initiative to reduce carbon emissions by 40% by the year 2040.
Engineering Innovation from Coast to Deep Ocean
Product innovation and technical leadership are cornerstones of Teledyne Valeport’s success. Presentations from Ian Slade, Head of Product Innovation, and Amy Thompson, Innovation and Product Manager, showcased a wide range of smart technologies engineered to survive and perform in some of the world’s harshest marine environments.
Key highlights included:
-
CTD Instruments (measuring Conductivity, Temperature, and Depth) used for profiling ocean water columns or monitoring fixed points, with models like the MIDAS CTD and SWiFT CTD capable of operating to depths of 6,000 metres.
-
Sound Velocity Sensors, such as the ultraSV and SVP, use time-of-flight acoustic technology to measure the speed of sound in water, a critical parameter for accurate sonar and underwater navigation.
-
Environmental Sensors in the Hyperion range, which use fluorescence to detect chlorophyll a, phycocyanin, crude oil, fDOM, and more. These are vital tools for water quality monitoring and pollution detection.
-
Tide and Water Level Monitoring via the TideMaster system, which integrates both pressure and radar sensors for flexible, accurate deployment. Portable and permanent installations are available.
-
Smart Data Features, including Bluetooth connectivity, GNSS positioning, and automated winch compatibility, allow users to collect and geo-reference environmental data with minimal manual handling.
The Bigger Picture: Made in the South West
Also in attendance were Tony Matteravers from Made in the South West and Jason Pitt, CEO of Made in Group. Jason shared insights into the origins and purpose of the group:
“Made in the Midlands was born as an editorial section in a regional newspaper, but really started to gain traction after the collapse of Rover. For the first time since the 1970s, people could see the ripple effect down the supply chain.
I’m passionate about building a channel of communication between local businesses that’s authentic and rooted in pride, especially at a time when the very foundations of what makes a nation great are being challenged.”
Final Reflections
The Teledyne Valeport factory tour was more than just an event—it was a deep dive into a company that embodies British manufacturing at its best. From nurturing apprentices to designing world-leading sensors, Valeport combines innovation, culture, and sustainability in a way that few can match.
Our thanks to the entire Teledyne Valeport team for hosting us and sharing their story. They continue to be not just a founding member of Made in the South West, but a shining example of what’s possible when technical excellence meets long-term vision.
If you’d like to host a tour or learn more about future events, get in touch with the Made in Group team.