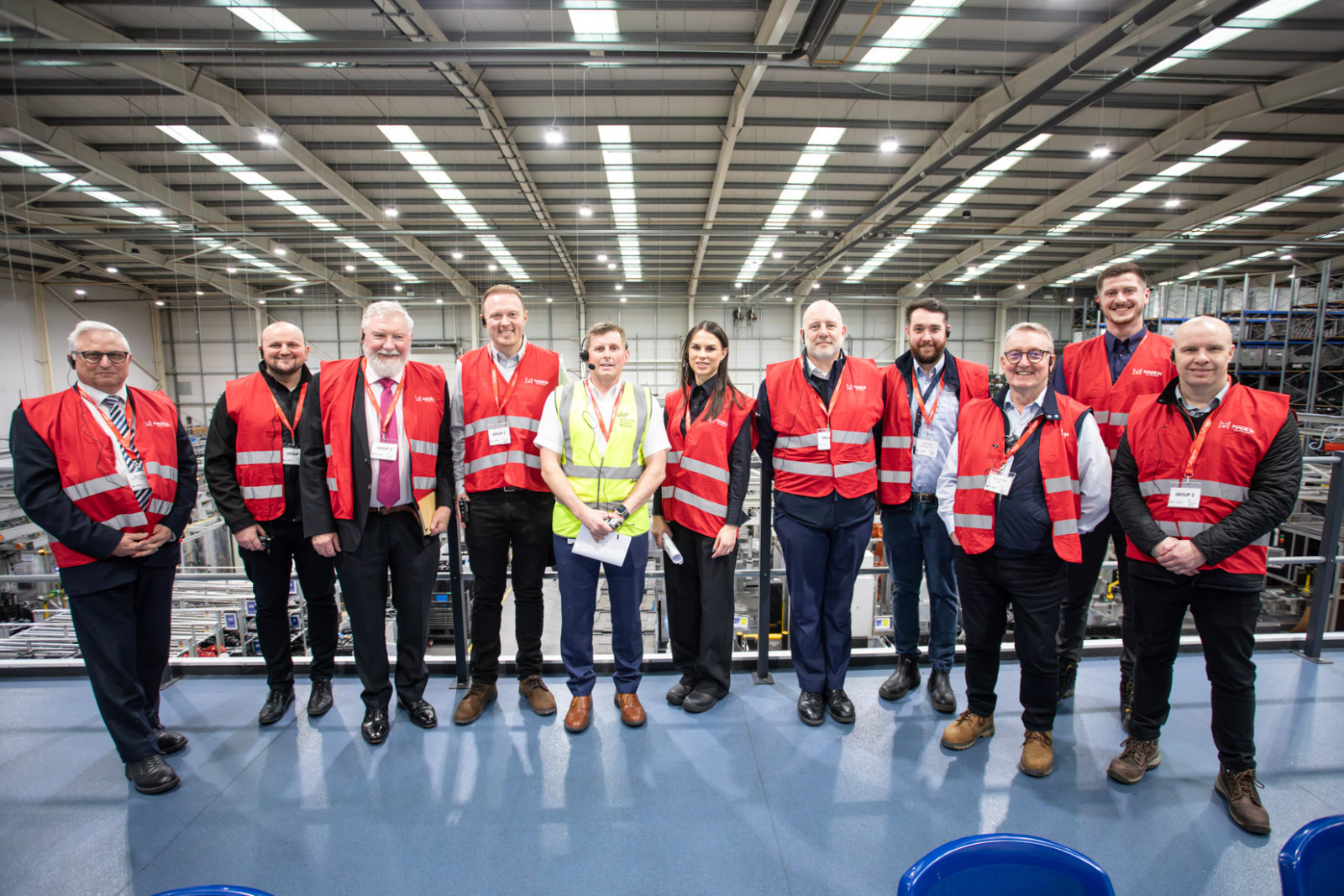
Factory Tour at ZF Foxconn Chassis Modules Highlights Industry-Leading Efficiency
Members of Made in the Midlands congregated at the ZF Foxconn Chassis Modules (ZFFCN)plant in Solihull for a highly anticipated factory tour. Organised by Made in the Midlands and facilitated by Plant Director Adrian Chell, the visit provided an up-close look at ZFFCN’s state-of-the-art facility. Attendees gained valuable insights into how a global technology leader in driveline and chassis systems operates at peak efficiency.
Founded in 2024, ZF Foxconn Chassis Modules is a 50-50 joint venture between ZF Friedrichshafen AG and Foxconn (Hon Hai Technology Group), the global assembler of the Iphone. ZF, a world-renowned company with expertise in driveline and chassis technologies, boasts a long history of delivering innovative mobility solutions to global automotive giants. ZFFCN stems from a former ZF product line and therefore can draw on 30 years of experience in the field of axle system assembly. The Solihull site specifically focuses on producing advanced chassis modules to meet the ever-evolving demands of the automotive sector. With high-profile customers relying on just-in-sequence (JIS) deliveries, ZFFCN’s Solihull operations stand out for their meticulous execution and streamlined workflows—attributes strongly emphasised throughout the tour.
From the moment the group arrived, the facility’s disciplined structure was evident. Visitors were greeted by well-organised workstations, clearly delineated walkways, and digital boards displaying real-time production metrics. As the tour kicked off, Adrian Chell welcomed everyone with a brief introduction: “Here at ZF Foxconn Chassis Modules Solihull, our primary focus is on quality, safety, and efficiency. Every system we have in place is designed to maximise productivity, ensure the highest product standards, and deliver on-time results for our customers.”
Made in the Midlands, a manufacturing membership group dedicated to promoting industry collaboration across the region, had arranged the tour to showcase best practices in automotive manufacturing. Jason Pitt, CEO of the Made in Group, offered high praise for the site’s smooth operations, noting that ZFFCN embodies an exemplary level of manufacturing excellence: “ZFFCN’s Solihull facility runs like a finely tuned machine, and that is largely thanks to Adrian’s unwavering commitment to refined processes and his meticulous organisational skills. Every corner of this plant—every procedure—is carefully planned to achieve both speed and precision.”
Tour participants included professionals from various engineering and manufacturing backgrounds, all eager to glean new ideas for their own operations. The event’s structure allowed them to observe production lines at different stages of development, highlighting how ZFFCN utilises lean manufacturing principles and cutting-edge machinery to craft chassis modules. Guided by Adrian and his passionate ZFFCN plant team members Steve Shinton, Simon Hunt, Darren Whitehouse and Fiona Turner , the visitors learned about the crucial role JIS processes play in ensuring that each module is completed and shipped in the precise sequence required by the company’s customers—often prestigious automotive brands that operate with tight production schedules of their own.
During the walkthrough, Adrian explained how these JIS processes dovetail with another core element of the ZF Group’s success: continuous improvement. “We’re constantly refining what we do here,” he said. “Whether it’s tweaking a workstation layout to reduce employee strain or implementing new software to track component usage, we always look for small changes that can lead to larger efficiency gains. The automotive market is incredibly competitive, and our goal is to stay one step ahead by integrating best practices into every aspect of production.”
Attendees were particularly impressed by the level of employee engagement on the shop floor. Operators were trained to follow robust quality control measures, utilising digital tools that monitor key performance indicators in real time. Adrian highlighted that no matter how advanced the machinery might be, human skill and communication remain critical: “Our success depends on our people. We invest heavily in training programs, ensuring everyone understands not just their individual tasks but how they fit into the bigger picture. This awareness fosters accountability, makes problem-solving more dynamic, and ultimately helps us deliver exceptional quality.”
In one area of the plant, visitors observed robotic arms deftly assembling components with astounding speed and precision. Sensor-based systems provided immediate alerts if any deviations from specified tolerances occurred, prompting quick intervention and adjustment. Adrian pointed out how this synchronicity between automation and human oversight leads to minimal downtime and optimal consistency in parts production. He also emphasised that while automation can handle routine tasks, ZFFCN believes in maintaining a skilled workforce that can interpret data and oversee processes to avoid potential pitfalls before they escalate.
Throughout the tour, several members of Made in the Midlands asked questions about supply chain strategies, sustainability initiatives, and workforce development. Adrian provided candid and practical responses. On sustainability, for example, he mentioned that ZFFCN continuously seeks ways to reduce waste, conserve energy, and integrate eco-friendly practices, explaining: “Beyond just meeting industry standards, we want to proactively set benchmarks for environmental responsibility. This includes re-evaluating packaging materials, employing energy-efficient equipment, and recycling wherever possible. We’re part of a global network that shares knowledge and innovation, which allows us to keep raising the bar.”
For many attendees, the highlight of the visit was witnessing the plant’s live demonstration of just-in-sequence deliveries: completed modules were moved from the assembly line directly onto waiting trucks, organised in the exact order required by the customer’s own production schedule. This flawless orchestration underscored how ZFFCN’s attention to detail translates into tangible benefits for car manufacturers: timely deliveries, reduced inventory costs, and improved responsiveness to shifting market demands.
At the conclusion of the tour, participants gathered for a short debrief, during which Jason Pitt reiterated the purpose behind organising such events. “Part of our mission at Made in the Midlands is to facilitate learning and collaboration,” he said. “We want our members to see how industry leaders like ZF Foxconn Chassis Modules drive continuous improvement. Observing real-world applications of lean principles and advanced automation can spark new ideas for everyone here, no matter the size or scope of their own businesses.”
Looking ahead, both ZFFCN and Made in the Midlands expressed optimism about future partnerships. For ZFFCN, hosting such tours fosters openness and transparency, while showcasing their position as a best-practice leader in automotive manufacturing. For Made in the Midlands, it furthers the organisation’s goal of promoting regional growth and ensuring that innovative methods permeate the local supply chain. By the end of the day, attendees left armed with fresh insights into the transformative power of methodical processes, forward-thinking leadership, and a dedication to continuous improvement—all of which make ZFFCN’s Solihull facility a shining example of industry-leading precision.