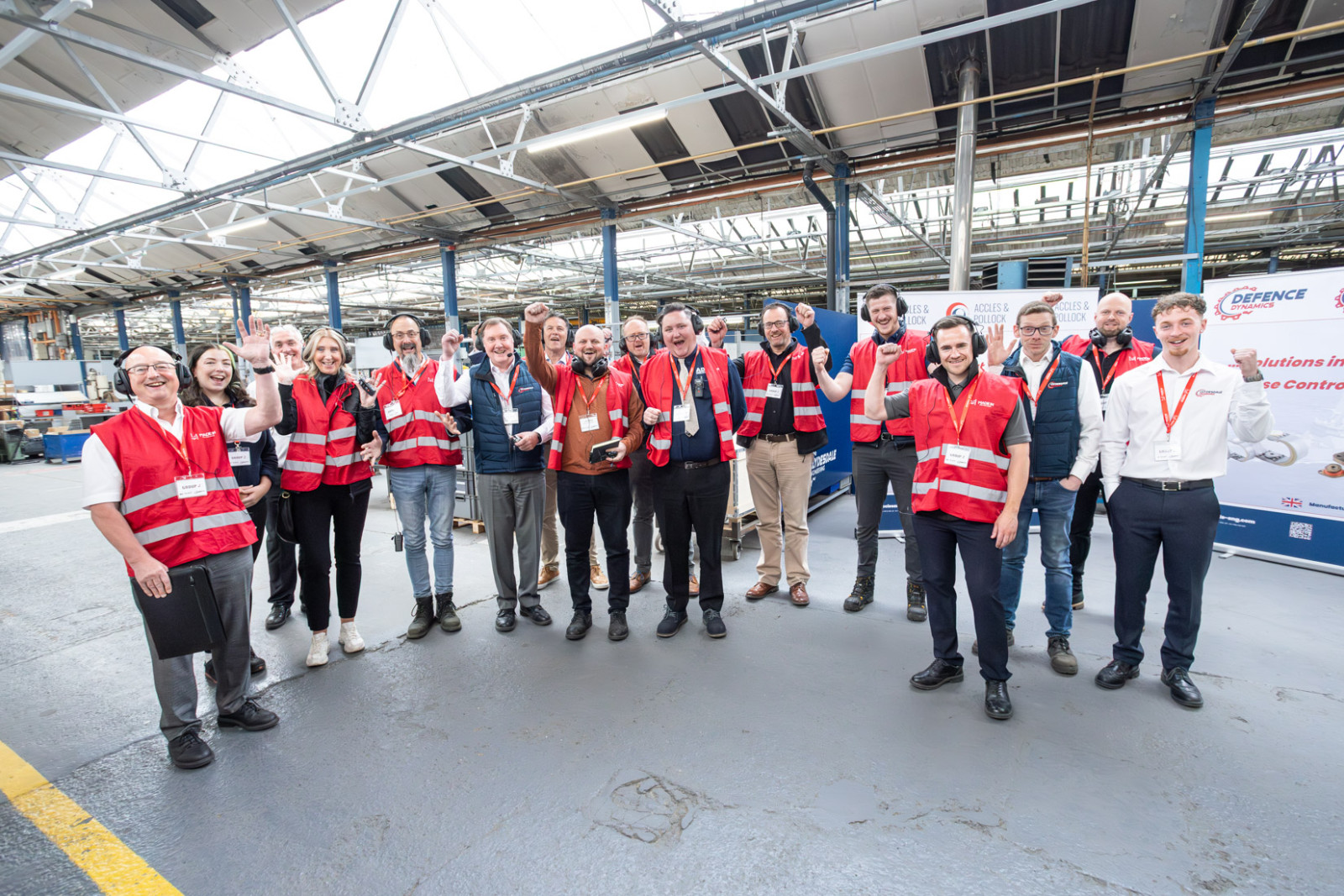
Clydesdale Engineering: Innovation, Simplicity, and British Engineering Excellence
Recently, members of Made in the Midlands had an exclusive opportunity to visit the historic site of Clydesdale Engineering, gaining valuable insights into best practices, innovative thinking, and teamwork within the engineering sector. The guided factory tour, led by Engineering Director Paul Everist, showcased a thriving business with deep roots in British manufacturing, underscoring the value of simplicity and adaptability in a complex, ever-evolving industrial environment.
Paul Everist, Engineering Director
Clydesdale Engineering is known for its multifaceted operations, spanning automotive, off-highway, aerospace, and defence sectors. The firm’s capabilities include precision press work, fabrication, pedal assemblies, and niche specialisms such as carbon fibre production. Their brands include the renowned Ackles and Pollock, established in the late 19th century and famed for precision tube manufacturing. Paul highlighted, “Accles and Pollock have a rich heritage of precision—some of the tubes we produce are incredibly small, yet vital for high-performance applications. It's a testament to our meticulous engineering standards.”
The site in question, sprawling across 45,000 square meters, is an engineering powerhouse, manufacturing over 7.8 million parts annually for nearly 200 global customers across 27 countries, including Japan, the USA, India, and South Korea. Products range from intricate automotive components for Lotus, Honda, Nissan, and Jaguar Land Rover to robust off-highway assemblies for leading brands like JCB and John Deere
One notable area of expertise showcased during the tour was the company’s involvement in shock and vibration solutions, especially critical in defence applications. Defence Dynamics, though perhaps less visible to the public eye, plays a vital role in naval safety, producing anti-shock mounts capable of reducing explosive shock from 200g forces to a manageable 15g, ensuring critical naval equipment remains operational under severe conditions. Paul noted, “Our Defence Dynamics solutions might not be widely known, but they are absolutely critical. We engineer reliability into extreme environments, safeguarding crucial naval capabilities.”
The factory’s versatile approach was evident in their adaptive methodologies. With a diverse range of products and sectors, Clydesdale Engineering emphasises simplicity in processes, despite the inherent complexity of their outputs. Paul explained, “Complexity can be a barrier to efficiency. Our approach is about maintaining simplicity and clarity wherever possible, even as we handle sophisticated engineering projects.” This pragmatic approach was highlighted through examples such as the rapid deployment of production lines following a client's urgent need. When a major customer's existing supplier went into administration, Clydesdale Engineering swiftly stepped in, setting up production within ten days—significantly faster than typical industry timelines. Such responsiveness underscores their flexibility and customer-centric ethos.
Simon Scott, Amada UK looking pleased to have spotted one of his machines on site
Flexibility is embedded not only in their strategic planning but physically in the layout of their facilities. Visitors noticed equipment and assembly fixtures placed on wheels, facilitating rapid reconfiguration and adjustment of factory spaces to meet fluctuating production demands. Paul commented, “Flexibility is essential. Our ability to quickly adapt our workspace allows us to remain responsive and efficient, adapting swiftly to changing requirements.”
Furthermore, the ethos of simplicity extends deeply into their manufacturing philosophy. Paul emphasised maintaining appropriate complexity controls: “Different products demand different approaches. Aerospace components naturally require exhaustive checks, but simpler products benefit from streamlined processes. Understanding this balance is crucial.” This intelligent discernment of complexity levels is vital in managing their vast portfolio effectively.
Teamwork at Clydesdale Engineering transcends departmental boundaries. The tour highlighted several instances of cross-functional collaboration, including engineers stepping into production roles during peak demand periods and different sector teams exchanging ideas to optimise processes. Paul proudly remarked, “Teamwork here is fundamental. Our success comes from leveraging collective expertise across departments. It’s truly collaborative innovation.”
Continuous improvement was a recurring theme throughout the tour. Despite a century-old history and significant legacy, Clydesdale Engineering remains keenly aware of ongoing improvement opportunities. Paul candidly acknowledged operational challenges: “We’re always mindful of continuous improvement. Even with our storied history, we focus on incremental improvements with clear benefits. It’s a disciplined, targeted approach that keeps us ahead.” Rather than attempting wholesale changes simultaneously, the company targets manageable improvements with clear, impactful outcomes—a strategy that aligns perfectly with lean manufacturing and agile principles.
Jason Pitt, Made in the Midlands, Paul Everist, Clydesdale Engineering and Ilona Pitt, Made in the Midlands
Clydesdale Engineering’s success illustrates how embracing simplicity, nurturing flexible operations, and fostering a strong collaborative culture can yield outstanding results in complex industrial environments. By prioritising adaptability and innovation, the company continues to thrive, maintaining an essential role in supporting and advancing British industry. Paul concluded, “Our heritage drives us forward, but it’s innovation and teamwork that ensures our future. We are proud to contribute actively to the strength of British engineering.”