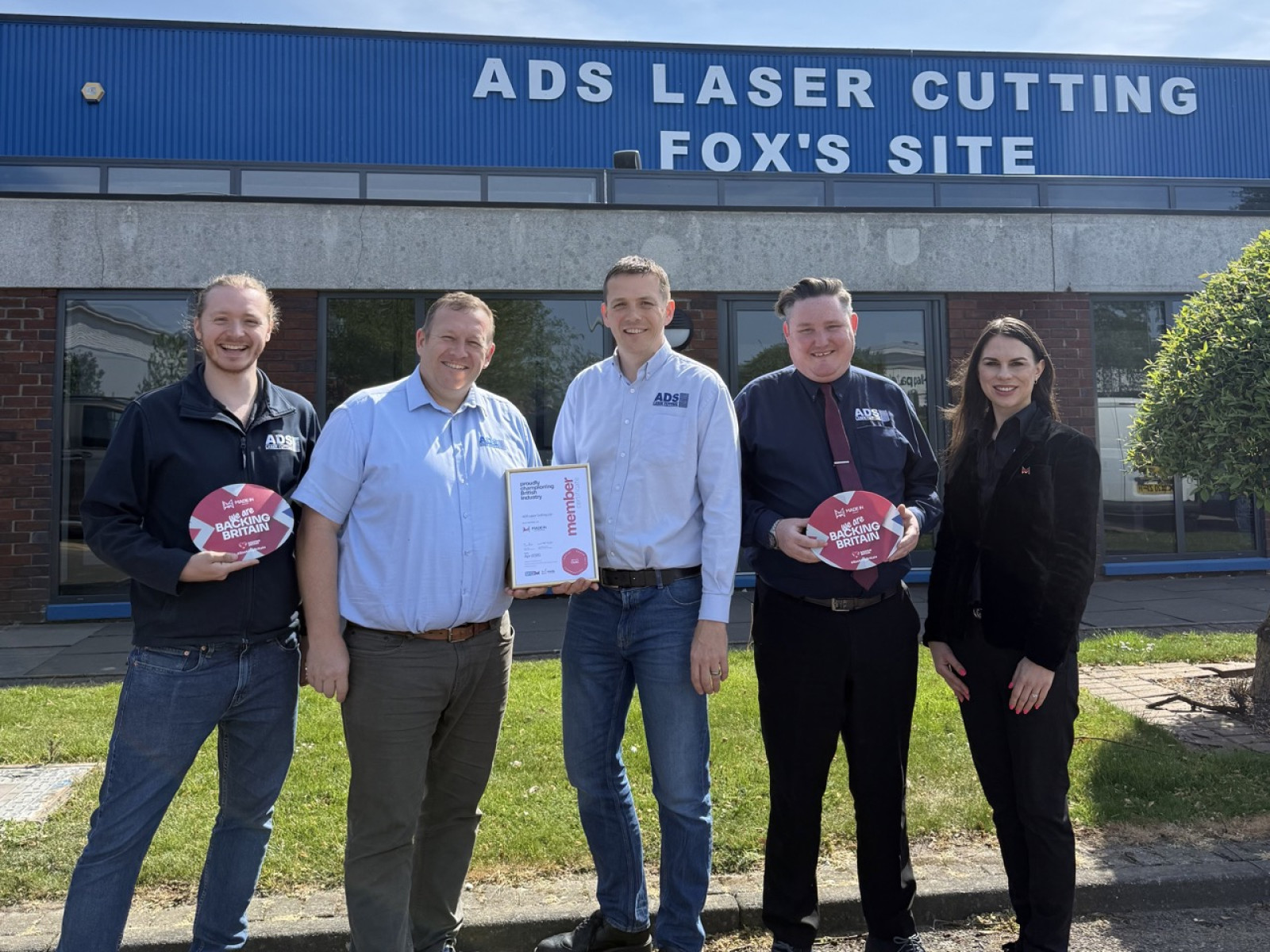
20 years of metalwork mastery โ step inside ADS Laser Cutting
From a modest 3,000 sq ft workshop in 2005 to a cutting-edge 87,000 sq ft manufacturing hub today, ADS Laser Cutting has evolved over nearly 20 years into one of the UK’s leading metalwork companies. Founded by brothers Duncan and Stephen Keates, alongside their wives Angela and Samantha, ADS has grown through bold decisions, continuous investment, and a commitment to quality.
A journey of growth and resilience – nearly 20 years of progress
Leicester’s rich manufacturing heritage forms the backdrop to ADS Laser Cutting’s remarkable journey. Established on Frog Island in 2005 with a single laser cutter, the company quickly expanded, moving to a 22,500 sq ft facility in Wigston just two years later – a clear signal of their long-term vision.
A defining moment came in 2010, when ADS acquired Altec, evolving from a specialist laser cutting provider into a full-service metalwork powerhouse, adding folding, fabrication, finishing, and assembly to its capabilities. This transformation enabled ADS to deliver a complete manufacturing solution under one roof.
In 2020, ADS took a bold step, relocating to the iconic former Fox’s Glacier Mints site in Leicester – an 87,000 sq ft facility on a seven-acre plot. This move, made during the uncertainty of the pandemic, consolidated operations and significantly increased production capacity. Reflecting on this pivotal moment, Stephen Keates, co-founder and director, said, "We’ve always believed in pushing boundaries. This site gave us the space to keep growing and investing in our people and technology."
Co-founder and director Duncan Keates echoed this sentiment: "It was a risk, but it has paid off. It gave us the flexibility to expand our services and set us on the path to continued growth."
Investing in people and technology
ADS’s success is built on its 100-strong workforce, including skilled fabricators, CAD cam, engineers, CNC operators, welders, engineers, and apprentices. The company launched its own apprenticeship programme 12 years ago and now works in partnership with Leicester College, nurturing the next generation of skilled metalworkers. Many of these apprentices have since progressed into senior roles, reflecting ADS’s commitment to career growth and internal development.
"We invest in people because that’s where the real value lies," said Stephen Keates. "A laser cutter can do amazing things, but it’s the people behind it that make the real difference."
Recent investments include high-precision laser cutters, robotic laser welders, and expanded finishing capabilities, positioning ADS at the forefront of UK manufacturing. This forward-looking approach has allowed the company to take on more complex, high-value projects while maintaining a focus on quality.
"We aim for zero MCRs (manufacturing corrective reports) or NCRs (nonconformance reports)," added Stuart Rowan, sales and marketing director. "That means our quality has to be right first time, every time."
Comprehensive capabilities under one roof
ADS Laser Cutting is more than its name suggests. The journey from raw metal to finished product begins in the cutting department, where powerful 10 kw fibre lasers slice through materials from thin-gauge aluminium to 40mm stainless steel, handling up to six-meter sheets. This precision cutting capability makes ADS a trusted partner for industries as diverse as aerospace, construction, and architectural metalwork.
"It’s not just about cutting metal," said Stuart Rowan. "We add value at every stage, from the moment a raw sheet arrives to the moment a finished, painted, assembled product leaves our factory."
After cutting, components move to the bending and welding areas, where ADS’s 640-tonne, six-meter press brakes and robotic welders handle everything from intricate profiles to heavy-duty structural parts. The recent addition of laser welding has been a game-changer, allowing ADS to achieve precision welds faster and more consistently than traditional methods.
Once parts are cut, formed, and welded, they pass through the finishing department, where they are shot blasted and coated, or polished. ADS offers a wide range of finishing options, from powder coating and wet painting to graining and polishing, ensuring each component leaves the facility ready for immediate installation.
The final stage is assembly, where components come together to form finished products, from intricate architectural brackets to full-scale EV charging posts and 1,000 balconies annually for major construction projects. For projects requiring secure, long-term storage, ADS provides secure CCTV-monitored outdoor space, offering peace of mind to its customers.
See ADS in action – factory tour on 10th July
Curious to see what an 87,000 sq ft metalwork powerhouse looks like up close? Join us for an exclusive factory tour at ADS Laser Cutting on 10th July. Witness cutting-edge lasers in action, explore end-to-end production capabilities, and meet the team driving their success.
As Ilona Pitt, director of Made in Group, puts it, "ADS Laser Cutting is a powerhouse of British manufacturing, offering far more than just laser cutting. It’s companies like ADS that drive innovation and set new standards for the industry, creating opportunities for growth and collaboration within our network."
๐
Factory Tour – ADS Laser Cutting
๐๏ธ 10th July 2025
๐ Fox's Site, Sunningdale Rd, Leicester LE3 1UE
๐ Book your place: madeinyorkshire.com | madeinthemidlands.com
Don’t miss this chance to connect with fellow manufacturers, share ideas, and see one of the UK’s most comprehensive metalwork facilities in action.